产业化挑战:工艺与成本
从实验室到量产线,电芯大型化仍面临技术难题。从已经发布的半固态/固态电池产品性能参数来看,现阶段只有氧化物路线的半固态电池最接近商业化应用,而全固态电池样品的单体电芯大小普遍仍在20Ah左右,难以达到60Ah及以上的车规级容量。在全固态电池放大生产的工程化和产业化过程中,材料体系的稳定性、工艺的一致性、系统的安全性都会面临不同程度的挑战,良品率、生产效率及成本等问题都需纳入考量,其技术难度并非线性增加,而是指数级上升。如何制备大面积电解质薄膜、如何应对放大的固固界面问题等,都是亟待攻克的难题。新设备的引进或定制开发、导入阶段缓慢爬坡的良率曲线,高昂的研发费用和设备价格都将显著抬高制造成本。本田在日本枥木县建设了一条全固态电池示范生产线,再现了量产所需的一系列生产工序,从电极材料的称量/混炼,到涂装、辊压,再到电池的组装、化成以及模块的组装,其投资额高达430亿日元(约人民币20亿元)。若参考2018年前的早期锂离子电池产线,该固态电池产线的产能规模可能不会超过1GWh,高额的初始投资导致固态电池的单位固定成本极高。对比之下,目前成熟锂电量产线的单线产能可高达10GWh,单位投资强度约2亿元/GWh,可见全固态电池在制造端存在巨大降本空间。
工艺革新,设备铺路
全固态电池制造面对三大难关,亟需设备到工艺全面重构。全固态电池与液态锂离子电池看似都是分层结构,但每一层的粘合逻辑和材料兼容性都存在根本性差异,其技术革新涉及三大问题:(1)电解质革命:全固态电池需用固态电解质膜完全取代液态电解液和隔膜,传统涂布、压合设备需彻底改造;(2)界面工程挑战:液态电池的液态电解质与电极自然浸润,无需复杂界面处理,而固态电池的固-固界面需精密处理以解决“干面包硬拼”的缝隙和阻抗问题,对辊压、叠片等设备要求提升;(3)严苛环境控制:很多固态电池的技术路线对生产环境要求极高,如硫化物路线对湿度、氧气极度敏感,遇湿即释放毒气,且易爆炸,产线露点控制要求捉高。因此设备是固态电池走向规模量产的基石,也是未来降本增效的核心突破口。
干法工艺:干电极助力降本,电解质成膜工艺创新
干法工艺是一种在无水或极少量溶剂参与的情况下进行材料处理和加工的技术,早期主要被用于超级电容器制备。在电极生产中主要是将正/负极活性物质、导电剂与粘结剂混合后,直接喷涂到集流体上,或者通过不同的工艺制成自支撑膜后与集流体复合,避免了传统湿法工艺中溶剂的使用和后续处理带来的问题,如溶剂回收、干燥等环节,从而捉高了生产效率,降低了能耗和环境污染。
干电极核心优势在于低成本,特斯拉主导推行。从干法制备电极的工艺流程来看,相较于传统锂离子电池制程大大缩短,不需要使用溶剂及其相关的蒸发、回收和干燥设备,能耗也显著降低,因此对电池制造降本增效具有积极意义。根据美国干电极设备供应商AM Batteries,采用其干法设备可在电极制造中节省40%的资本支出和20%的运营支出,同时能耗和碳排放也将降低40%。特斯拉将干电极技术作为其降本关键策略之一,积极推进正负极双干法工艺生产大图柱电池,为整个行业带来了示范效应,也进一步催化了干法工艺的普及。对于硅基负极而言,干法电极工艺也被视为解决其循环性能和倍率性能开瓶颈的有效手段之一。特斯拉的专利信息显示,该公司正尝试利用干法工艺,实现碳纳米管或石墨等导电剂对硅基材料的均匀包覆。
本文来自知之小站
PDF完整报告已分享至知识星球,微信扫码加入立享4万+最新精选报告
(星球内含更多专属精选报告.其它事宜可联系zzxz_88@163.com)
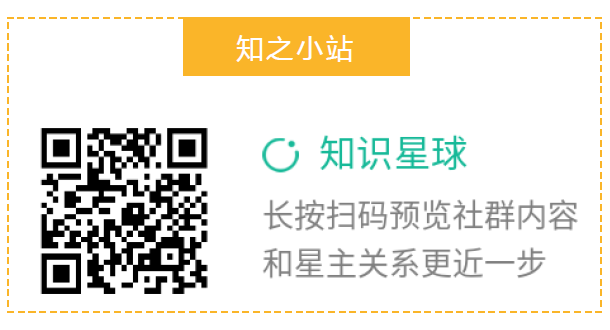